CMTI or CMIT?
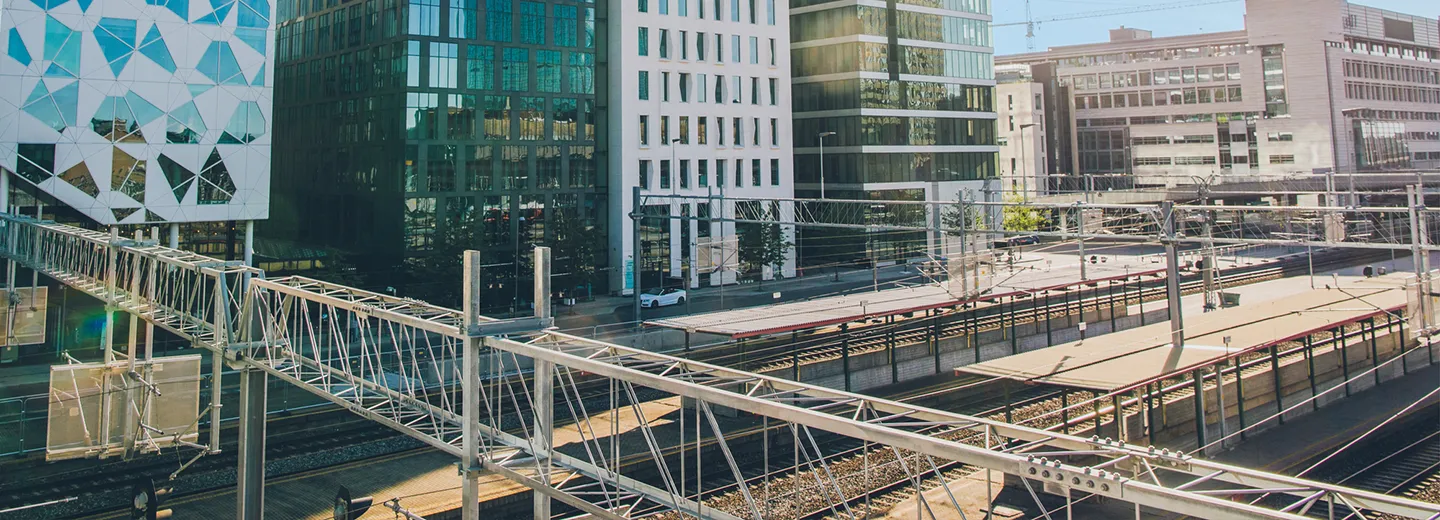
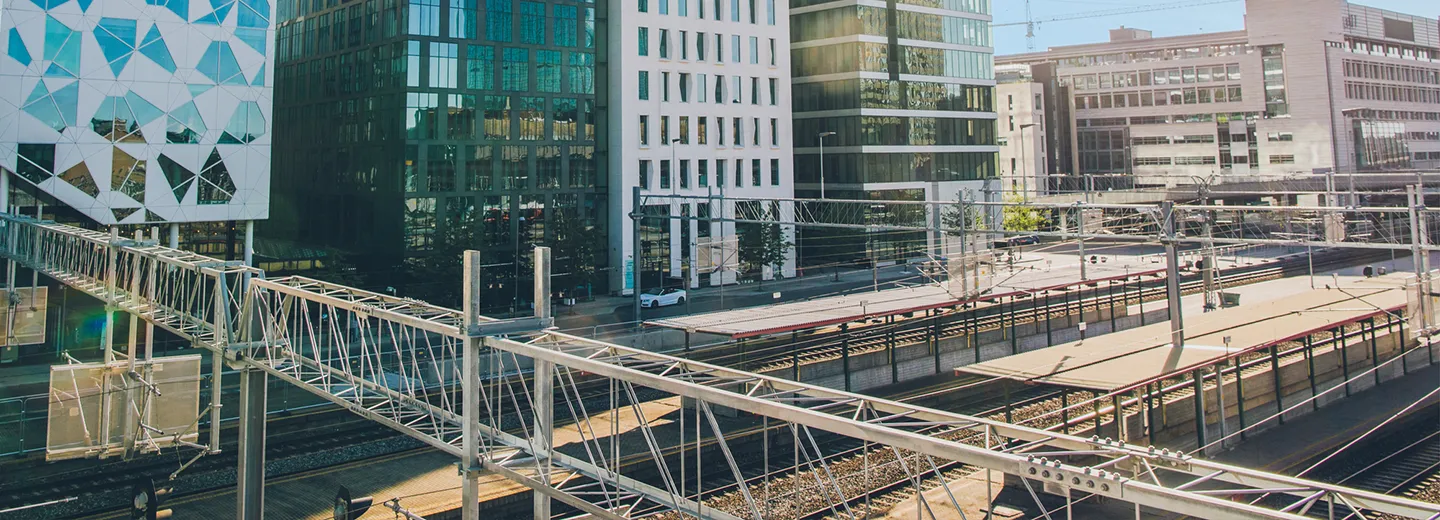
For those in our industry the acronym CMTI represents Construction Materials Testing and Inspection. However in recent years it often seems as if the T and I have flipped to IT due to the heavy amount of Information Technology that is used on a daily basis.
It wasn’t so long ago that when a proposal was needed, or inspections were performed in the field, that our team would receive actual paper plans/specifications to review or inspect off of, but now paper plans are becoming more and more rare. The ease of file sharing through Dropbox, Box, and other similar providers, as well as the advent of the iPhone and iPad and every other smart phone or tablet that has followed in their footsteps has resulted in many projects going almost, if not completely, paperless. Another contributor to this phenomenon is that many projects are built at a much faster pace and therefore the plans are not yet finalized so waiting on someone to print and distribute paper plans would simply delay the project.
Many of our inspectors have generated their reports electronically for years, but these reports have been in many formats (Word, Excel, PDF, etc.), which resulted in reports that did not look consistent from one inspector to the next. Paper copies of the electronic versions were often still generated by on-site or portable printers, and the paper version of the reports were what were actually distributed to the project team. These paper versions of electronically written reports did not allow for any intelligent capture of data so that the data can be easily searched.
As we have endeavored to stay current with changes in technology within the construction industry, we have encountered several challenges. When transitioning to electronic reporting these challenges included the following:
- Fear of technology (both by the user and those reviewing or receiving the reports)
- Compatibility of devices and programs (is it iOS or Android, can our database interact with your database, etc.)
- Competing services (Box or Dropbox, eBuilder or Skire Unifier, etc.)
- Application based or Web based
- Internet access in the field
As a solution to the issues noted above, Twining is in the process of implementing company-wide a program called QESTField. QESTField is a web based field reporting program that is accessed by our inspectors from any internet connected device (smartphone, tablet, laptop, etc.). QESTField communicates with our laboratory information management system (LIMS), QESTLab, and allows our field staff to generate their reports electronically, register field made specimens that will need to be tested in the laboratory, obtain client signatures, and save the information directly into QESTLab. Once the information is saved it is immediately available to Twining project managers for review and distributed to project team members. Lab sample information is also already in QESTLab which allows for lab staff to process samples and report results more quickly. QESTField allows for the field information that previously may have taken over a week to distribute to all team members and makes it available to project team members almost in real time.
Our initial roll-out began with a small group of inspectors in mid-August. We will begin pushing out this tool to the remainder of our field inspection staff in November with the goal of having all inspectors using QESTField by the end of January 2017.
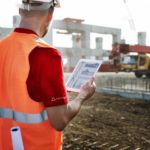
Should you have any questions regarding this exciting new technology please contact me. linasvitkus@twininginc.com
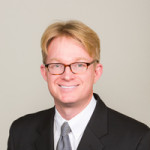
Linas Vitkus is a civil and geotechnical engineer and serves as Twining’s Senior Vice President of Operations. Before beginning his career as an engineer, Linas worked nights and weekends during high school driving the Zamboni machine at his local ice skating rink. Linas received his Bachelors degree from UCLA in both Civil and Environmental Engineering. He started his career as an engineer, and he joined Twining in 2006, as a Civil Engineer. He was quickly promoted to Twining’s Director of Laboratory Operations, and then to Senior Vice President of Operations. Linas also serves as Project Manager on many of Twining’s high profile projects, including the Port of Long Beach’s $1.31 billion Middle Harbor upgrade, as well as the Wilshire Grand, and multiple projects for UCLA, UCI, and Kaiser, and over 100 DSA projects in Southern California. Linas specializes in working on projects from the initial planning and conceptualization phase through to final design and construction. He also provides operational management of Twining’s five offices and laboratories throughout California. In what little downtime he has, Linas enjoys spending time with his wife and two sons playing soccer and Lithuanian school on Saturdays.