Alkali-Silica Reaction (ASR): Understanding the Effects of ASR in Concrete Structures
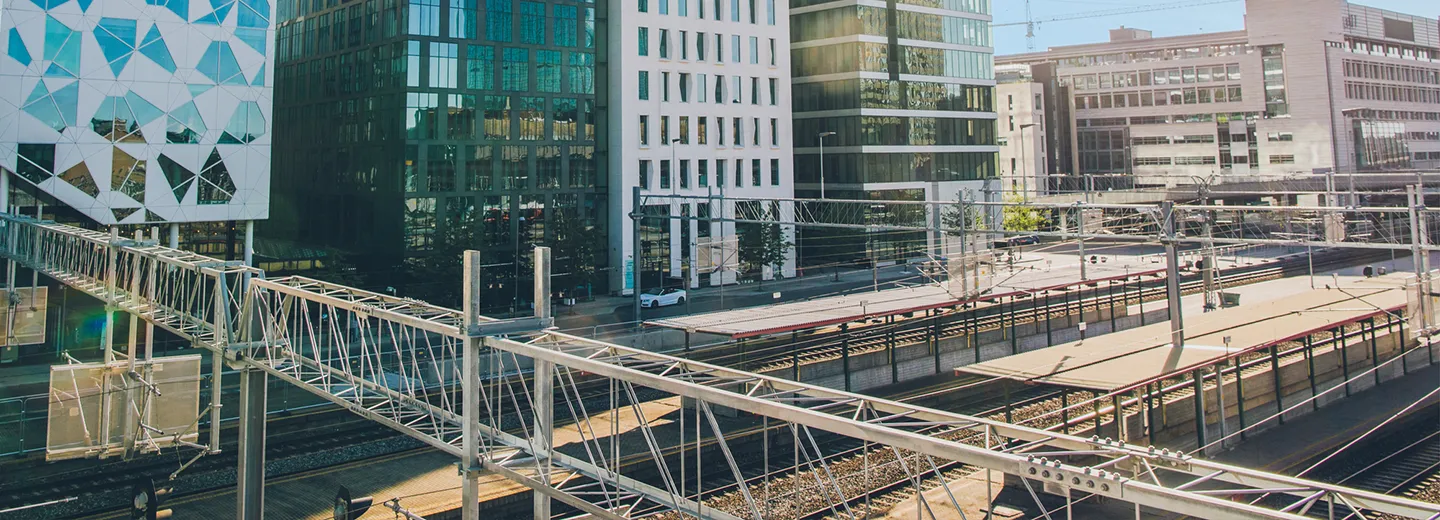
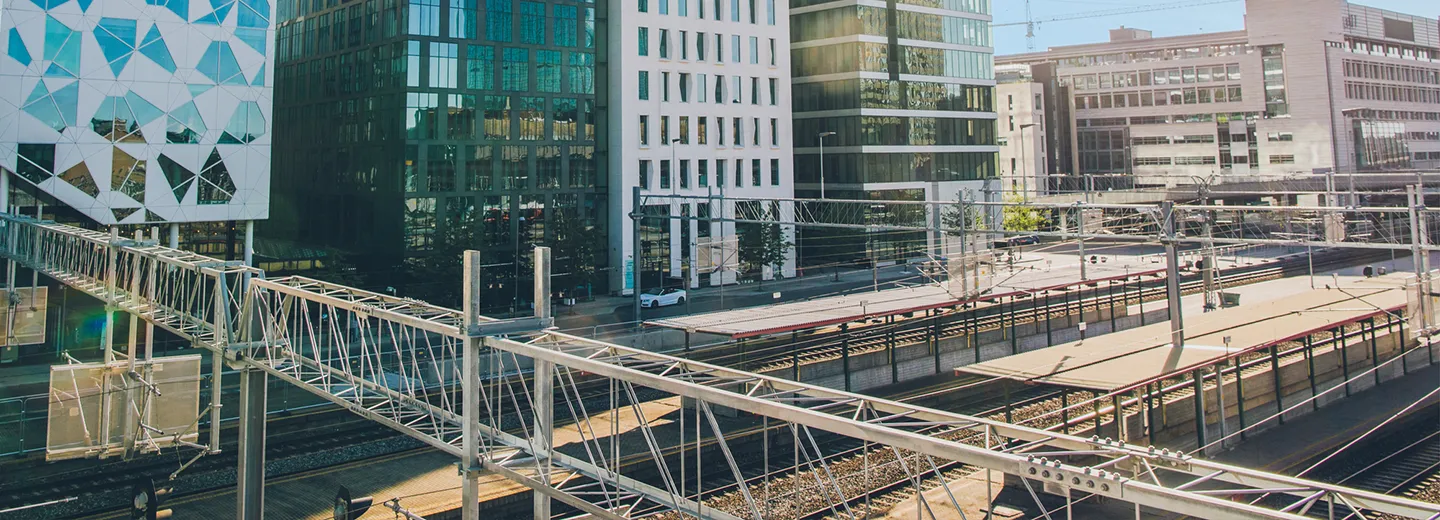
Alkali-Silica Reaction (ASR)
What is it, how to characterize it using destructive and non-destructive techniques, and why petrographic examination is the most useful tool for understanding the effects of ASR in concrete structures.
Meredith Strow, PG, Principal Petrographer and Director of Petrographic Services
Alkali-Silica Reaction (ASR) in Concrete
Alkali-silica reaction (ASR) was first identified by Thomas Stanton approximately 80 years ago and is now considered to be one of the most common and damaging deterioration mechanisms observed in concrete structures [1]. ASR occurs when alkaline pore solution in the paste fraction reacts with unstable silica in the aggregate fraction to form a gel. The formation of ASR gel causes expansion in concrete and can result in cracking and deterioration of concrete structures. ASR gel reveals itself as colorless to white deposits circumscribing reactive aggregate particles, extending outwardly from reactive aggregate particles in microcracks and macrocracks, filling pore space within the paste microstructure, and lining to filling voids within the concrete. ASR deterioration can manifest as cracking or white deposits on exterior surfaces. These features can be documented in condition evaluations as they can be observed with the unaided eye. Many tests have been developed to aid in the understanding of the reaction and how to mitigate the reaction in concrete. First, it is important to understand concrete as a material and its components.
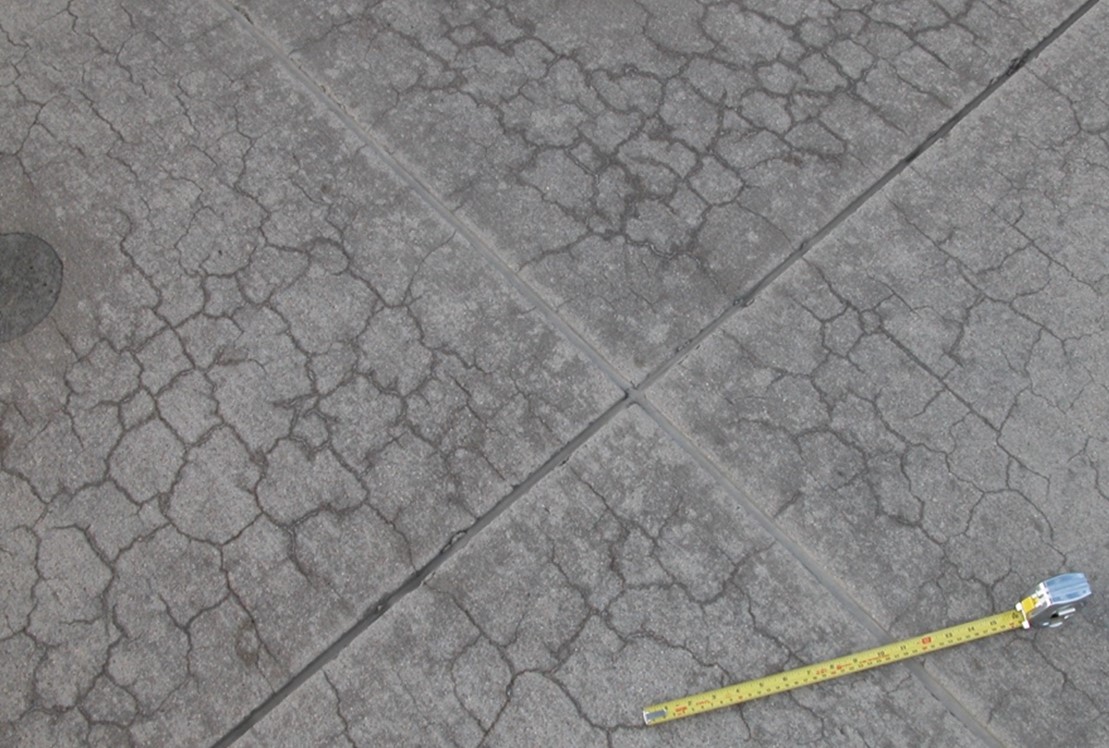
In general terms, concrete is formed when cement, coarse aggregate, fine aggregate, and water are combined. Mix constituents may also include supplementary cementitious materials (SCMs) and admixtures (air entraining, water reducing, hydration stabilizing, set retarding, etc.). The combination of cement with mixing water creates a paste that binds aggregate particles together. The paste is formed by calcium silicates, supplied by the cement, which react with mixing water to form calcium silicate hydrates (CSH) and other hydration products. Cement is alkaline in nature and contains Na2O and K2O. Pore solution, or moisture present in concrete, typically consists of dissolved alkalis (sodium Na+, potassium K+) leached from the cement fraction of the concrete. External sources of moisture (i.e. rainwater) and alkalis (i.e. deicer salts) can affect the chemistry of the pore solution. Moisture and alkali content each play an important role in the ASR deterioration mechanism [2-6].
ASR deterioration is characterized by three main stages: 1) reaction of alkaline pore solution and siliceous aggregate, 2) formation of gel, and 3) concrete expansion as the gel absorbs and retains moisture [5]. The reaction begins between pore solution and aggregate when there are sufficiently high levels of sodium hydroxide and potassium hydroxide in the pore solution and unstable silica in the aggregate [3]. Hydroxide ions cleave bonds of unstable silica (SiO2) in aggregate particles, followed by embedding of Na+ and K+ into the silica matrix to form ASR gel [5]. Finally, ASR gel absorbs moisture, swells, and ultimately causes expansion in concrete. It is important to note that the ASR deterioration mechanism has been described, but not all concrete that experiences ASR gel formation experiences deterioration (cracking) [3].
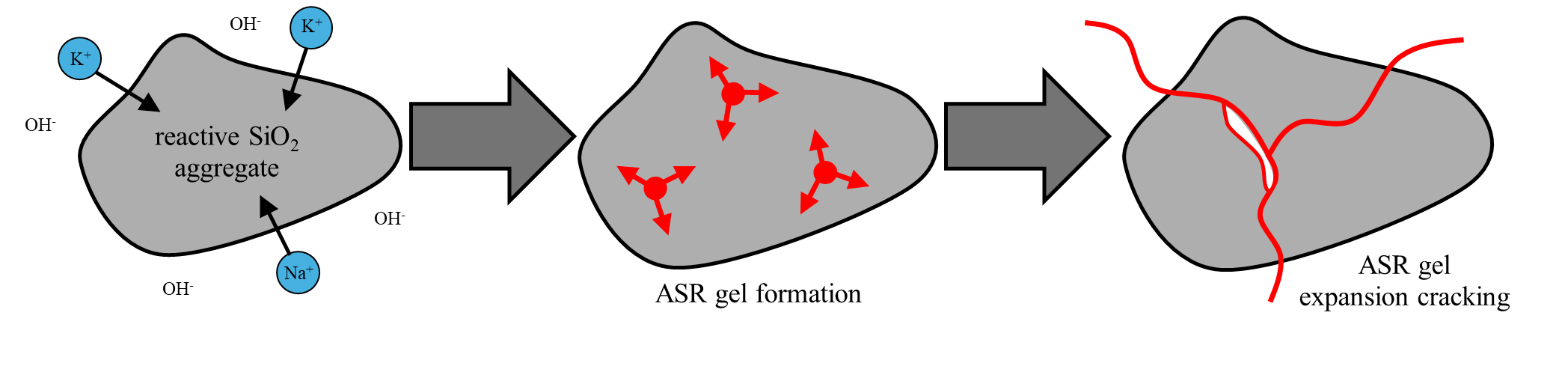
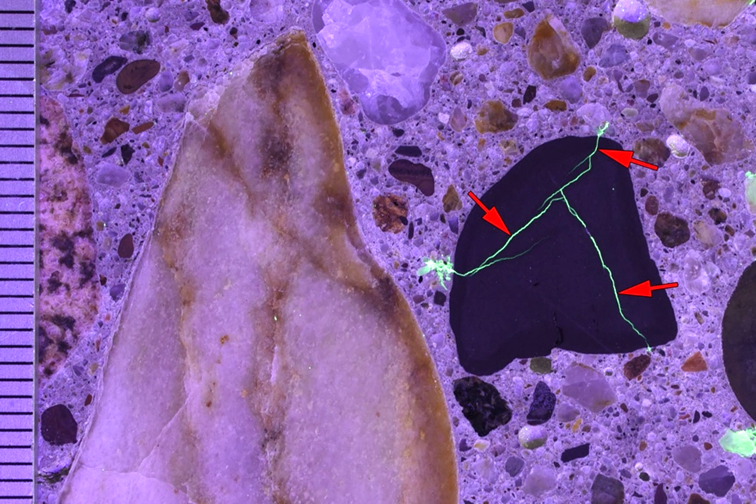
Although many studies have been conducted to understand ASR and develop accelerated tests for concrete mixture evaluations, the reaction can still occur even when the mixture is qualified with such tests. For example, aggregates could be qualified using ASTM C1260 or ASTM C1567 accelerated mortar bar testing (AMBT) or ASTM C1293 concrete prism testing (CPT). However, the mix might not perform well in the field, or when the deleterious nature of the aggregate has gone unidentified in laboratory testing. ASTM C295, a petrographic examination of aggregate for concrete [7], is a useful test for identifying the presence of potentially alkali-silica reactive aggregate particles in samples obtained from quarries and pits. Also, ASR still occurs when SCMs, such as fly ash, are incorporated into the mix with the intent of ASR mitigation.
For economic reasons, the type of aggregate used in concrete is generally local to the geographic region in which the structure is built. However, rock types vary by geographic location and, therefore, a variety of aggregates are used in concrete structures around the world. Silicates make up the largest portion of rock-forming minerals on this planet. However, silica (SiO2) is found in many forms including quartz and quartzite, strained quartz, microcrystalline or cryptocrystalline quartz (e.g. chert and chalcedony), volcanic glass (e.g. cristobalite), and other forms of amorphous silica (e.g. opal) [8]. The type of reactive silica may be present as chert within cherty limestone in one geographic location whereas in another location the reactive silica may be present as strained quartz within a metamorphic gneiss particle. Proper identification of aggregate types and their potentially deleterious nature are critical to reducing the chance of ASR deterioration in concrete.
Evaluation of ASR Using Destructive Techniques
Petrographic examination of concrete (ASTM C856) is a test method that is extremely valuable to condition evaluations and understanding the deterioration a concrete structure has experienced or is currently experiencing. The test method is the only test that identifies ASR in concrete. All other tests associated with ASR only document expansion or characterize the composition of pore solution within the concrete. Petrographic examination is a destructive test method that requires concrete samples to be extracted from in-situ structures. Although the test can be performed on batched concrete mixtures and related samples subjected to expansion testing, the test is mostly performed on samples from existing structures. Petrographic testing is the most effective way of identifying the presence of ASR gel in concrete and evaluating the extent of associated deterioration or damage. Results yield valuable information including aggregate rock type (lithology), determination of reactive rock types, qualitative amount of ASR gel, degree of deterioration (cracking), and related deterioration characteristics [9]. The analysis is qualitative in nature and may not be able to provide a prognosis for future expansion.
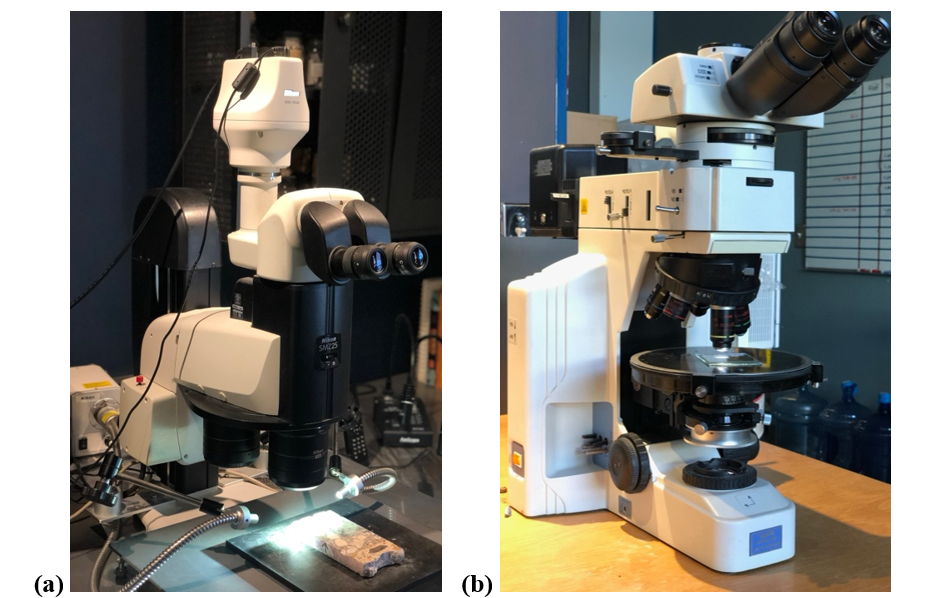
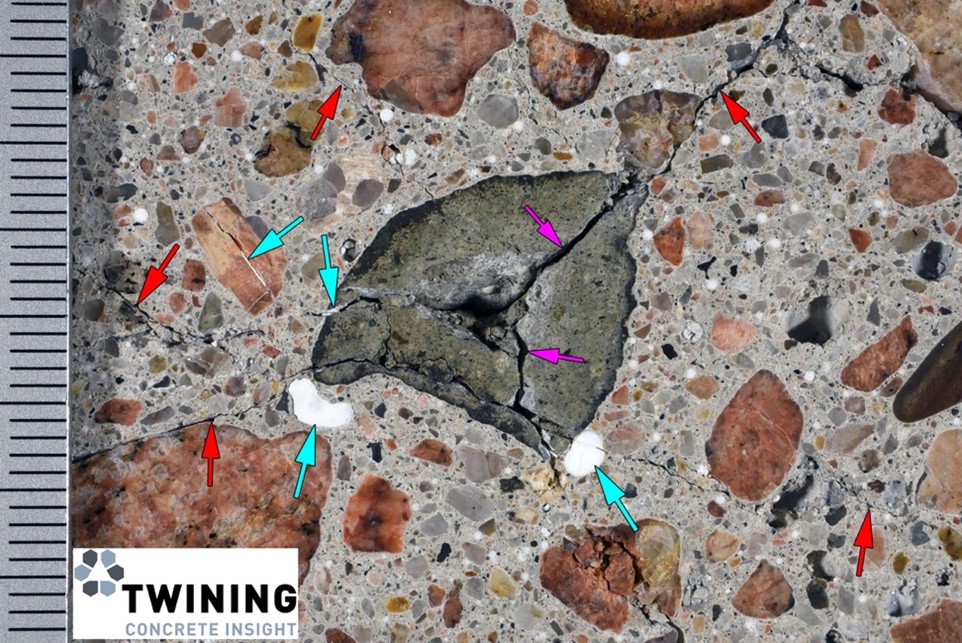
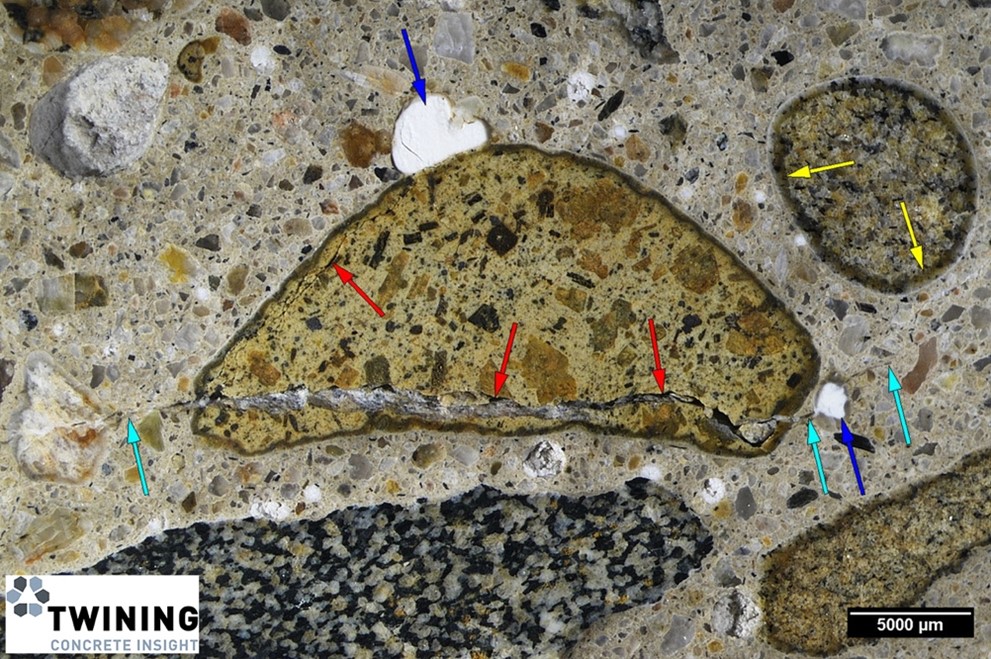
Petrographic examination is a qualitative test that can be performed in conjunction with damage rating index (DRI) testing to provide quantitative information for ASR evaluations. The DRI test method, described by Grattan-Bellew and Dunbar [10-11], quantifies the amount of ASR-related deterioration features present in a concrete specimen. This test method is often performed as supplemental testing to petrographic examination because it requires a polished concrete surface which is often prepared for petrographic examination. DRI is the most effective approach for quantifying ASR deterioration while also providing visual confirmation of ASR gel and its characteristics within concrete. Similar to the petrographic examination, this approach does not provide a prognosis for future ASR expansion.
Residual expansion testing, on the contrary, can provide ASR prognosis information. Fournier et al. proposed this destructive test method which involves extracting cores from ASR-affected structures and storing them in two types of conditions: 1) over-water in air at 95 percent or greater relative humidity (RH) and at 38°C (100°F), and 2) submerged in 1N NaOH solution at 38°C (100°F) [13]. These conditions are intended to represent the realistic expansion and residual reactivity of the concrete, respectively. The first condition replicates ASTM C1293, ‘Standard test method for determination of length change of concrete due to the alkali-silica reaction,’ testing conditions [12]. Length expansion measurements collected over the course of one year (% exp./yr) are used to predict the degree of concrete expansivity and aggregate reactivity. No other test method as of yet, either destructive or nondestructive, provides both diagnosis and quantitative prognosis of ASR using concrete from the active structure. In addition, Fournier et al. suggest supplementing residual expansion testing with water-soluble alkali testing of the concrete; this is also done destructively by obtaining core samples from the structure. The amount of water-soluble alkalis extracted from concrete allows for interpretation regarding whether or not the concrete contains enough alkalis to either produce ASR gel or to further ASR deterioration. Water-soluble alkali testing offers meaningful information for both diagnosis and prognosis assessments of ASR. Residual expansion testing is often conducted alongside petrographic examination and DRI testing for visual confirmation of ASR and correlation of data [13].
Evaluation of ASR Using Nondestructive Techniques
A variety of non-destructive techniques have been studied to aid in the evaluation of ASR deterioration. Nondestructive ASR testing can be divided into two groups: laboratory testing and field testing. Laboratory testing typically consists of preparing concrete samples within the laboratory, inducing ASR, and evaluating concrete properties and characteristics. This type of testing is helpful in qualifying materials for use in concrete and understanding how materials may perform in field conditions. Field testing consists of investigating in-situ concrete structures without damaging the integrity of the structure; no samples are removed, and the structure is not taken out of service. This type of testing supplies data that is specific to the structure, its materials, and the environment in which it exists; these variables are nearly impossible to recreate in a laboratory setting.
The three most common laboratory tests performed for evaluating alkali-silica reactivity of concrete constituents are 1) ASTM 1260: The standard test method for potential alkali reactivity of aggregates, 2) ASTM C1567: The standard test method for determining the potential alkali-silica reactivity of combinations of cementitious materials and aggregate, and 3) ASTM C1293: Standard test method for determination of length change of concrete due to alkali-silica reaction. ASTM C1260 and ASTM C1567 are considered accelerated tests due to the total testing period of 16 days, compared to that of ASTM C1293 testing which takes one to two full years [12, 14-15].
ASTM C1260 is an accelerated mortar bar test that evaluates a specific aggregate’s ability to react with typical Portland cement. The test uses one crushed and properly graded aggregate to produce at least three 1 x 1 x 11.25 in. mortar bars. The mortar bars, after curing, are submerged in sodium hydroxide solution for 14 days and length change measurements are collected to calculate percent expansion. ASTM C1260 states that a final percent expansion of less than 0.10% indicates innocuous aggregate reactivity behavior, a final percent expansion of greater than 0.20% indicates potentially deleterious aggregate reactivity behavior, and expansion between 0.10 to 0.20% is inconclusive because both aggregates known to be reactive, and aggregates known to be nonreactive have expanded within this range. If an aggregate fails ASTM C1260 testing, ASTM C1567 testing is commonly recommended to reevaluate the potential for reactivity with the use of ASR-mitigating supplementary cementitious materials, such as fly ash or slag [14].
ASTM C1567 is also an accelerated mortar bar test, but this test evaluates a specific aggregate’s ability to react with typical Portland cement in combination with supplementary cementitious materials, such as fly ash slag cement or natural pozzolan. Like ASTM C1260, the test uses one crushed and properly graded aggregate to produce at least three 1 x 1 x 11.25 in. mortar bars. The mortar bars, after curing, are submerged in sodium hydroxide solution for 14 days and length change measurements are collected to calculate percent expansion. ASTM C1567 states that a final percent expansion of greater than 0.10% indicates potentially deleterious aggregate reactivity behavior [15].
ASTM C1293 is the one-year-long equivalent of ASTM C1260 and the two-year-long equivalent of ASTM C1567. ASTM C1293 testing uses one crushed and properly graded aggregate with a known nonreactive counterpart (fine or coarse aggregate) to produce at least three 3 x 3 x 11.25 in. concrete prisms, or prisms. If the test is intended to determine the reactivity of a fine aggregate, a known nonreactive coarse aggregate is used in the concrete mix. Conversely, if the test is intended to determine the reactivity of a coarse aggregate, a fine aggregate known to be nonreactive is used in the concrete mix. The test can be performed on Portland cement concrete as well as concrete designed with supplementary cementitious materials. The concrete prisms are submerged in sodium hydroxide solution for one to two years and length change measurements are collected to calculate percent expansion. ASTM C1293 states that a final percent expansion of greater than 0.04% indicates potentially deleterious aggregate reactivity behavior. The standard also states that the expansion of less than 0.04% in prisms containing Portland cement after one year and in prisms containing Portland cement and supplementary cementitious materials after two years is considered innocuous [12].
Another laboratory test that aids in the evaluation of aggregate reactivity is ASTM C295: Standard guide for petrographic examination of aggregates for concrete. This test is performed by identifying the rocks and minerals within an aggregate (coarse or fine), per ASTM C294 descriptive nomenclature, and quantifying the amount of each observed rock lithology for a total classification of the aggregate sample [7, 16]. Deleterious rock types and particles containing potentially reactive mineralogy are quantified with the intent of providing engineers, quarries, and ready-mix producers information to help understand the characteristics of the material and its potential limitations for use in concrete or other building materials. For example, a limestone aggregate may contain individual chert particles or limestone particles containing chert; the total weighted percent of chert and particles containing chert would be reported because chert consists of microcrystalline quartz which is potentially reactive with the alkalis in Portland cement. ASTM C295 testing is commonly performed prior to ASTM C1260, ASTM 1567, and ASTM C1293 testing because results indicate whether or not potentially reactive particles exist within an aggregate sample.
Field testing of in-situ structures for ASR evaluation can be performed nondestructively by one or more, but not limited to, the following field techniques: visual observation, acoustic shear wave tomography, length expansion sensor monitoring, acoustic emissions (AE), ultrasonic testing (UT), Electrical impedance spectroscopy (EIS), and microwave testing. Visual observation of cracks, white ASR gel deposits, or both, is the most straightforward and inexpensive nondestructive technique. However, it takes a trained eye to discern ASR gel from other types of white secondary deposits such as ettringite and calcium carbonate efflorescence and it may not be possible to differentiate with the unaided eye. For this reason, petrographic examination of hardened concrete per ASTM C856 is the most effective and informative method for identifying and characterizing ASR in concrete structures.
The content in this blog post is largely recycled from Ms. Strow’s master’s thesis research work conducted in association with Argonne National Laboratory and the Materials Engineering Department of the University of Illinois at Chicago. Referenced and related work is listed below.
- Strow, Meredith L (2019). Nondestructive Evaluation of Alkali-Silica Reaction (ASR) in Concrete. University of Illinois at Chicago. Thesis.
- Heifetz, A., Strow, M., Liu, Y., Bevington, P., Zapol, P., Bahktari, S., and Bentivegna, A., 2020, Monitoring dielectric permittivity in accelerated alkali-silica reaction concrete with microwave backscattering, Materials and Structures, Vol. 53 (5).
- Strow, M., Bevington, P., Bentivegna, A., Bakhtiari, S., Aranson, I., Ozevin, D., and Heifetz, A., 2022, Monitoring accelerated alkali-silica reaction in concrete prisms with petrography and electrical conductivity measurements, Materials and Structures, Vol. 55(4).
- Koka, J. Argonne National Laboratory (2022, April 26). Argonne scientists discover new ways to diagnose cracks in concrete: A chemical reaction that causes concrete to crack and deteriorate can now be identified without harm, according to Argonne scientists [Press release]. Retrieved from https://www.anl.gov/article/argonne-scientists-discover-new-way-to-diagnose-cracks-in-concrete
Cited Literature
1. Stanton, T.E.: Expansion of concrete through reaction between cement and aggregates. Proceeding of the American Society of Civil Engineers 66:1781-1811, 1940.
2. Deschenes, D.J.: ASR/DEF-damaged bent caps: shear tests and field implications. Master’s thesis, University of Texas at Austin, Texas, 2009.
3. Detweiler, R.: The role of fly ash composition in reducing alkali-silica reaction. Portland Cement Association, Technical Report: PCA R&D Serial No. 2092, 1997.
4. Kosmatka, S. and Wilson, M.: Design and Control of Concrete Mixtures. Skokie, Illinois, Portland Cement Association 15; 208-212, 2011.
5. Rajabipour, F., Giannini, E., Dunant, C., Ideker, J., and Thomas, M.D.A: Alkali-silica reaction: current understanding of the reaction mechanism and the knowledge gaps. Cement and Concrete Research 76:130-146, 2015.
6. Snyder, K.A. and Lew, H.S.: Alkali-silica reaction degradation of nuclear power plant concrete structures: a scoping study. National Institute of Standards and Technology, Internal Report: NISTIR 7937, 2013.
7. ASTM Standard C295, 2019, "Standard guide for petrographic examination of aggregates for concrete," ASTM International, West Conshocken, PA, 2019.
8. Klein, C. and Dutrow, B.: Mineral Science. Hoboken, New Jersey, John Wiley & Sons, Inc., 23:536-539, 2008.
9. ASTM Standard C856, 2020, "Standard practice for petrographic examination of hardened concrete," ASTM International, West Conshocken, PA, 2020.
10. Dunbar, P.A., and Grattan-Bellew, P.E..: Results of Damage Rating Evaluation of Condition Concrete from a Number of Structures Affected by AAR. Proceedings of CANMET/ACI International Workshop on AAR in Concrete, Dartmouth, Nova Scotia, CANMET, Department of Natural Resources Canada, 257-265, 1995.
11. Grattan-Bellew, P.E.: Comparison of Laboratory and Field Evaluation of Alkali-Silica Reaction in Large Dams. Proceedings of the First International Conference on Concrete Alkali-Aggregate Reactions in Hydroelectric Plans and Dams, Fredericton, New Brunswick, Canada, 23 p., 1992
12. ASTM Standard C1293, 2023a, "Standard test method for determination of length change of concrete due to alkali-silica reaction," ASTM International, West Conshocken, PA, 2023.
13. Fournier, B., Berube, M., Folliard, K.J., and Thomas, M.D.A.: Report on the diagnosis, prognosis, and mitigation of alkali-silica reaction (ASR) in transportation structures. Federal Highway Association, Technical Report: FHWA-HIF-09-004, 2010.
14. ASTM Standard C1260, 2023, "Standard test method for potential alkali reactivity of aggregates (mortar-bar method)," ASTM International, West Conshocken, PA, 2023.
15. ASTM Standard C1567, 2023, "Standard test method for determining the potential alkali-silica reactivity of combinations of cementitious materials and aggregate (accelerated mortar-bar method)," ASTM International, West Conshocken, PA, 2023.
16. ASTM Standard C294, 2019, "Standard descriptive nomenclature for constituents of concrete aggregates," ASTM International, West Conshocken, PA, 2019.