The Nature, Importance, and Implementation of Charpy V-Notch Impact Testing in the Building Construction Industry
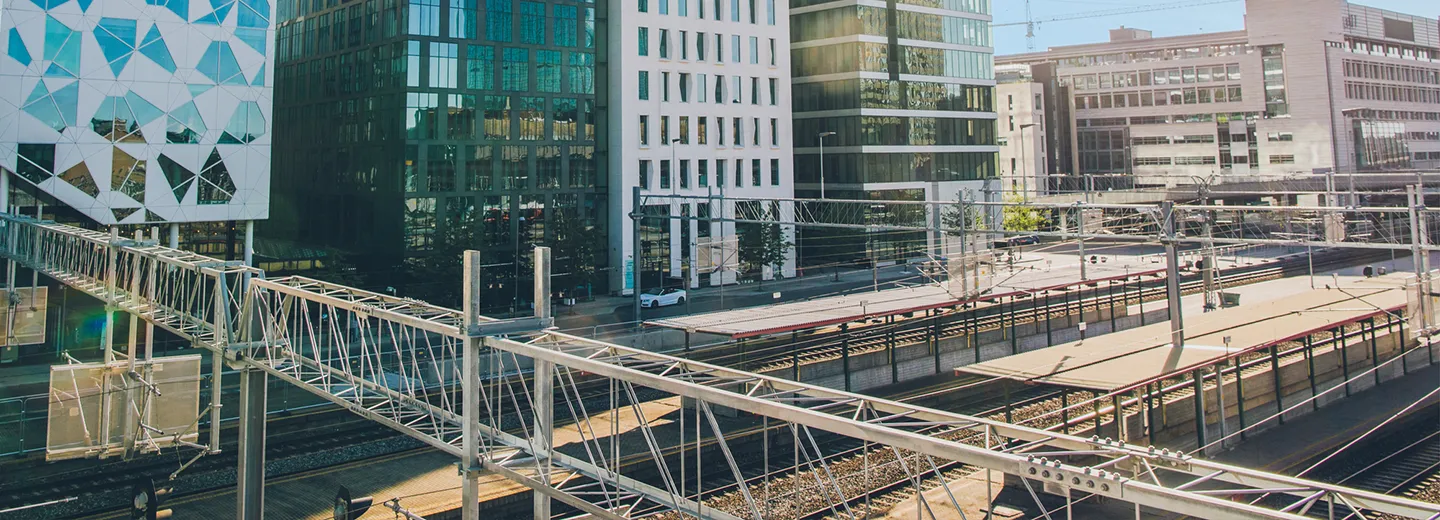
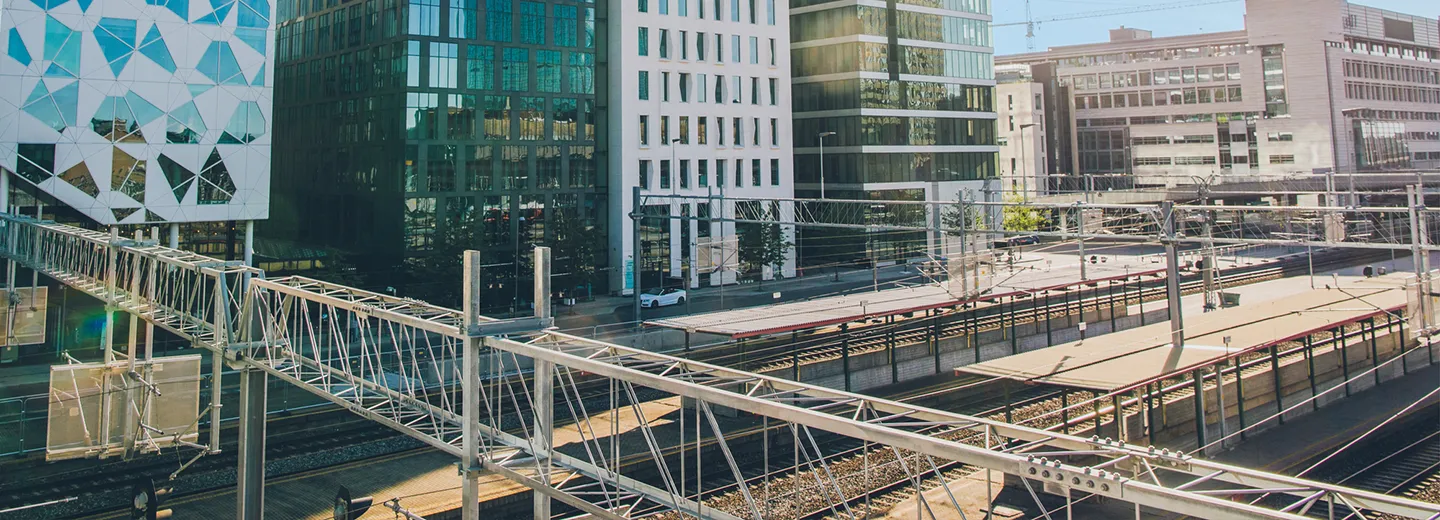
Introduction
The 1994 Northridge Earthquake was devastating to Southern California, with many buildings damaged beyond repair and significant loss of life. As is typical, the temblor also revealed some unexpected deficiencies in design and construction. In particular, steel moment frame buildings utilizing complete joint penetration (CJP) groove welds for beam-column connections had been thought to be quite resilient to earthquake forces. The earthquake revealed that this was not necessarily the case. Many such structures were found to be extensively damaged, and many such connections were found to be cracked and even completely ruptured.
Much research was performed to determine the cause or causes of these surprising consequences, and Twining was a participant in several of these research efforts. One of the assumptions of moment frame design was that the CJP welds would deform plastically under severe earthquake stresses, that is, they would absorb seismic energy by yielding (stretching) rather than fracturing.
Two terms used to describe the ability of a material to deform plastically without fracture are “ductility” and “fracture toughness,” and there are various ways to characterize and to measure this property. One method to measure this property is notch toughness testing, and the Charpy V-notch impact test is one of several such test methods.
The Nature of Charpy V-Notch Impact Testing
The Charpy V-notch impact test (CVN) is a standardized high-strain-rate test that determines the amount of energy absorbed by a material during fracture. The test involves striking a notched specimen with a pendulum hammer and measuring the energy absorbed in breaking the specimen. The pendulum hammer swings through an arc from a known height, and thus has a known gravitational potential energy, Upon striking the notched specimen, mounted at the bottom of the CVN apparatus, the hammer will lose energy in fracturing the specimen, and will rise to a lesser height on the far side of the test apparatus. The difference in height represents the energy absorbed by the notched specimen during the test. See the image below.
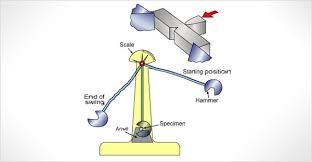
History and Development
Developed by Georges Charpy in the early 20th century, the Charpy impact test has become a fundamental method for assessing material toughness. Charpy's innovation was the introduction of a standardized notch, the V-notch, which concentrates stress and promotes fracture at a specific point, allowing for consistent and comparable results across different materials and tests.
Test Procedure
The Charpy V-notch test involves several key steps:
1. Specimen Preparation: The test specimen is a small bar, typically measuring 55 mm in length with a cross-section of 10 mm by 10 mm. AV-shaped notch with an angle of 45 degrees and a depth of 2 mm is machined into the middle of one face.
2. Mounting: The specimen is mounted horizontally in the testing machine.
3. Impact: A pendulum hammer, released from a fixed height, strikes the specimen on the opposite side of the notch.
4. Measurement: The energy absorbed by the specimen during fracture is recorded, usually in joules though, in the U.S., many specifications and standards use foot-pounds. Also recorded are measurements related to a visual analysis of the fracture surface.
Importance of Charpy V-Notch Impact Testing
The Charpy V-notch test is critical in the building construction industry for several reasons. It helps engineers and material scientists ensure that materials will perform reliably under various conditions, particularly in environments where they may be subject to sudden impacts or temperature variations.
Temperature Effects
Materials can behave differently at various temperatures. The Charpy test is often performed at different temperatures to determine a material's ductile-to-brittle transition temperature (DBTT). This information is vital for structures exposed to extreme cold, ensuring that materials remain ductile and do not become brittle and fracture-prone. For building construction, the test temperature is often based on the “lowest anticipated service temperature” (LAST). A typical specification would be a “minimum of 20 foot-pounds at -20° Fahrenheit.” However, we have seen requirements for testing at as low as -40° Fahrenheit.
Quality Control and Standards Compliance
The construction industry is governed by stringent standards and regulations. The Charpy V-notch test is a standard method referenced in many of these regulations, such as ASTM E23 and ISO 148. Conducting this test ensures that materials meet the required toughness specifications, providing a benchmark for quality control.
Implementation of Charpy V-Notch Impact Testing
Implementing Charpy V-notch testing in the building construction industry involves several stages, from material selection and testing to the interpretation of results and integration into the design process. Such requirements can be found in such standards as AWS D1.1 –Structural Welding Code, Steel, and AISC
Material Selection and Preparation
Materials intended for construction must be carefully selected and prepared for Charpy V-notch testing. This includes ensuring that the specimens are free from defects and representative of the bulk material. The notch must be precisely machined to the correct dimensions to ensure accurate and consistent results. ASTM and AWS codes and standards that specify locations from which material for CVN testing should be extracted.
Bridges and Infrastructure
In bridge construction, materials are subject to dynamic loads from traffic and environmental factors. CVC testing helps engineers select materials that can withstand these stresses without catastrophic failure. For instance, in the construction of the Akashi Kaikyō Bridge in Japan, one of the world's longest suspension bridges, materials were rigorously tested to ensure they could endure the harsh marine environment and seismic activity.
High-Rise Buildings
High-rise buildings face unique challenges, including wind loads, seismic activity, and the need for fire resistance. For locations like Los Angeles and its surrounding cities, and others on the Pacific Rim, the potential for major temblors is the driving consideration in specifying fracture toughness. The Charpy V-notch test is crucial in selecting materials that provide the necessary toughness to prevent brittle failure. For example, the Burj Khalifa in Dubai, the world's tallest building, utilized materials tested for toughness to ensure stability and safety under extreme conditions.
Computational Methods
Computational methods and simulations are becoming increasingly important in material testing. Finite element analysis (FEA) and other computational tools allow engineers to model and predict material behavior under various conditions, reducing the need for extensive physical testing. These methods can be used in conjunction with Charpy V-notch testing to validate and refine models, ensuring accurate predictions.
Conclusion
The Charpy V-notch impact test plays a vital role in the building construction industry, ensuring that materials can withstand the stresses and impacts they will encounter throughout their service life. By assessing material toughness, understanding temperature effects, and ensuring compliance with standards, this test contributes to the safety and reliability of structures.
As technology and materials continue to evolve, the Charpy V-notch test remains a cornerstone of material testing, complemented by advanced methods and computational tools. Together, these approaches provide a comprehensive framework for selecting and validating materials, ensuring that the built environment remains safe and resilient for future generations.
Twining is equipped and prepared to perform CVN testing and we have provided such testing on a large variety of projects, both for in-place construction and for research of methods of moment frame construction that have been designed to eliminate the likelihood of brittle fracture in the event of future seismic events. See the embedded video from MaterialsScience2000 to view an actual CVN test.